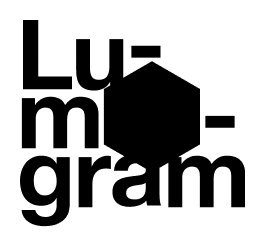
Lumogram is an interactive, backlit diorama pendant, made with environmentally-mindful materials (wood and paper) and bespoke, re-usable touch-activated electronic lighting.
Copyright 2024– Chuan Khoo
While the call for pilot testing is under way, the ‘V2’ edition (featuring the hexagonal pendant design) of the Lumogram is, at this time, NOT licensed under any Creative Commons license that the rest of this online resource is attributed to.
As the tangible component of an educational discovery workshop for young participants (16+), the goal is to demonstrate design through technology (touch-sensitive optics) and creative ideation (backlit dioramas). The cutout design’s flexibility also enables engaging with wider communities to craft customised thematic narratives with the help of templates. The backlit cutout designs enable a multitude of combinations to suit any theme.
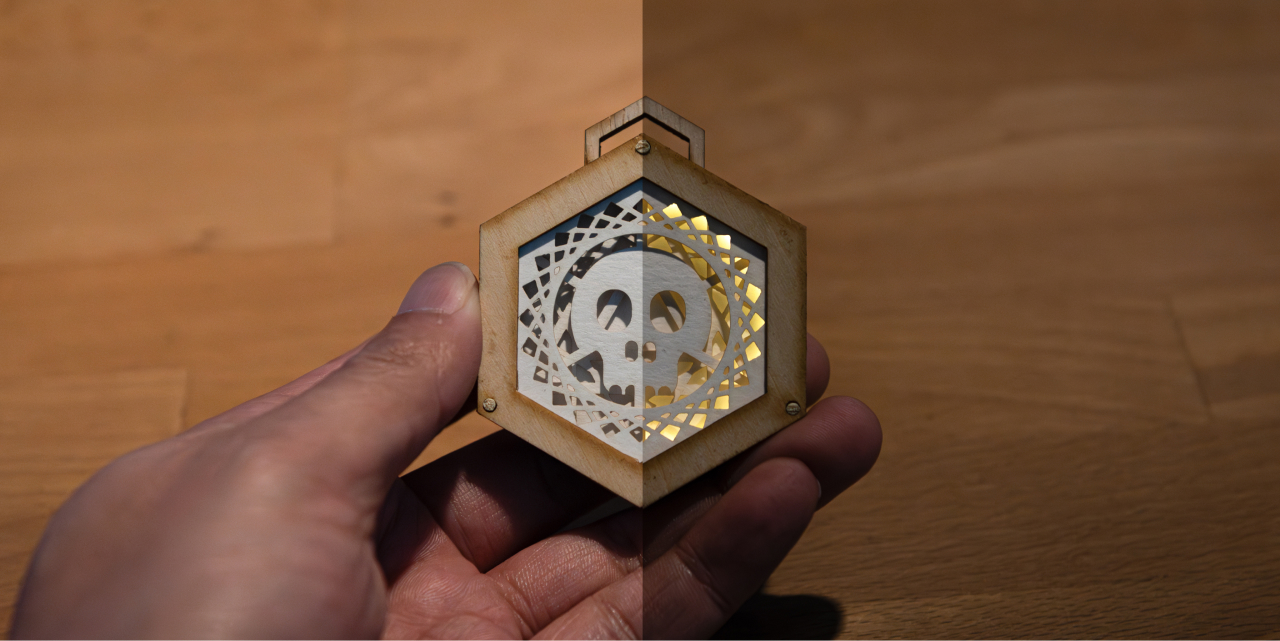
Lumogram, showing both lit and unlit states when touched from the rear cover.
As a creative practitioner working across digital, tangible interaction design and their related technologies, I adopted a transdisciplinary ethos to this project, to evaluate what it means to engage with slowness* in a technological creative practice. This meant working with material and technology as an integral process, affording active reflection during prototyping. In return, the practice invariably results in the design of products that reciprocate this focus: we value the craft and the self-curated possibilities that go into a product’s design.
Introducing an intriguing capacitance touch-sensing feature in the form of a pendant also allowed participants to appreciate the role design has, in considering technologies beyond typical ‘mainstream’ applications.
Lumogram’s design also minimises material loss by utilising waste offcuts as ‘accessories’ for the pendant, and optimised layout of the laser cut material.
* Further information
Chuan Khoo, “Slow Data in the Age of Digital Things: Designing Calm Interventions With Electronic Objects,” (Ph.D. diss., RMIT University, 2022.)
Lumogram’s now at Version 2!
The second edition of the Lumogram platform is out! It improves on the previous edition by adopting an updated form factor and optimised laser cuts to reduce material waste. It also features an integrated electronic touch-sensing and LED board to encourage easier re-use, resulting in less reliance on plastic compared to the V1 edition!
It continues to be held together by toothpicks, and a bit of glue :)
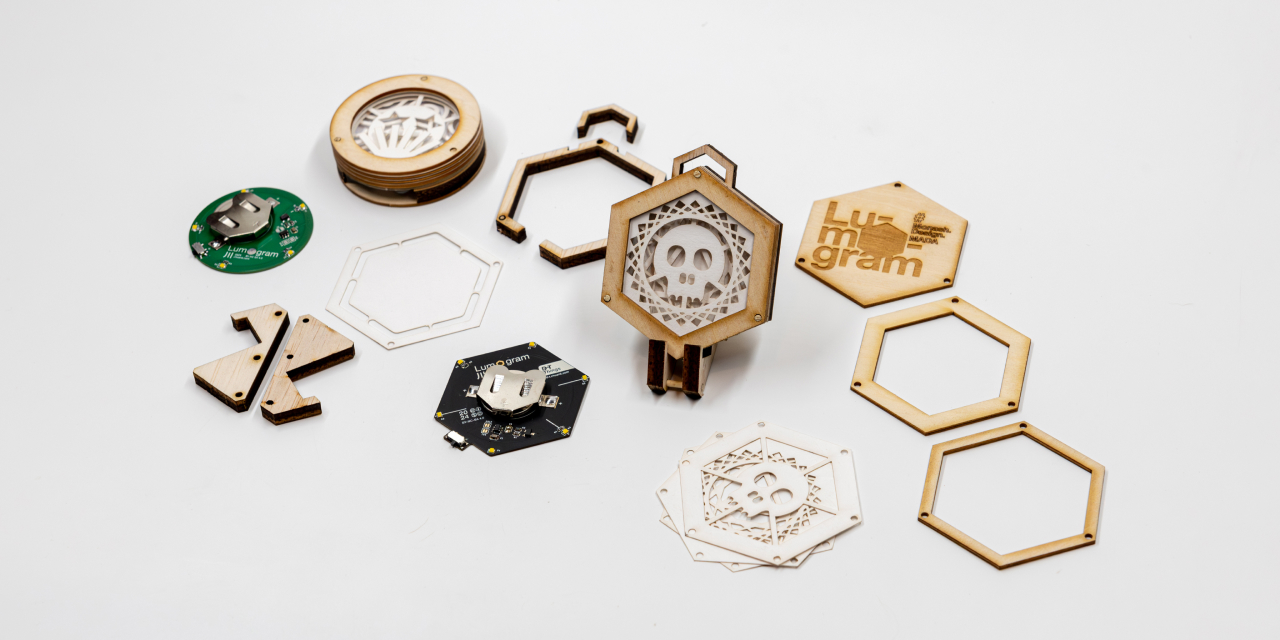
The main parts that make up a Lumogram V2, with the original V1 edition shown in the upper left along with a prototype circular PCB. Not pictured: toothpicks.
More details about the V2 Design » The original V1 Design »
Join our Pilot Program!
As a pilot test, we are opening the Lumogram workshop to high schools and communities wanting to work with the Lumogram’s technology and its supporting education materials. We are currently in the process of finalising the materials, and working out the best distribution model to do this. Please get in touch with me to find out more!
Acknowledgements
Keeping with the education ethos of the Lumogram project, the V2 edition was produced with the contribution of MADA interns. Prototype fabrication assistance was made possible by the MADA Digital Fabrication Lab (dFab).
Hopefully, this is a list that will continue to grow.
2024 Winter Edition
Manaporn “Pam” Tanwimonrat | V2 concept refinement & cutout graphic design, COLLECTION.01 | |
Gusti “Decha” Wigneshwara | V2 concept refinement, industrial design execution & exploded diagram animation |
I’d also like to acknowledge the following people for additional contributions to the project:
- MADA dFab – Ed Turner (V2) & Lindsay McKittrick (V1) for technical production support
- MADA Design – Nika Chayy (V2) for the 2024 kit production
- MADA Design – Prof. Gene Bawden for setting the initial design+technology brief, and supporting the Lumogram’s development
A new hexagonal form factor
A key requirement in the Lumogram V2 brief was to minimise waste material. This was achieved with a hexagonal design, which allowed for a honeycomb tiling pattern for the laser cut paths. This led to more usable cuts per sheet, and less energy spent by the laser going over shared paths.
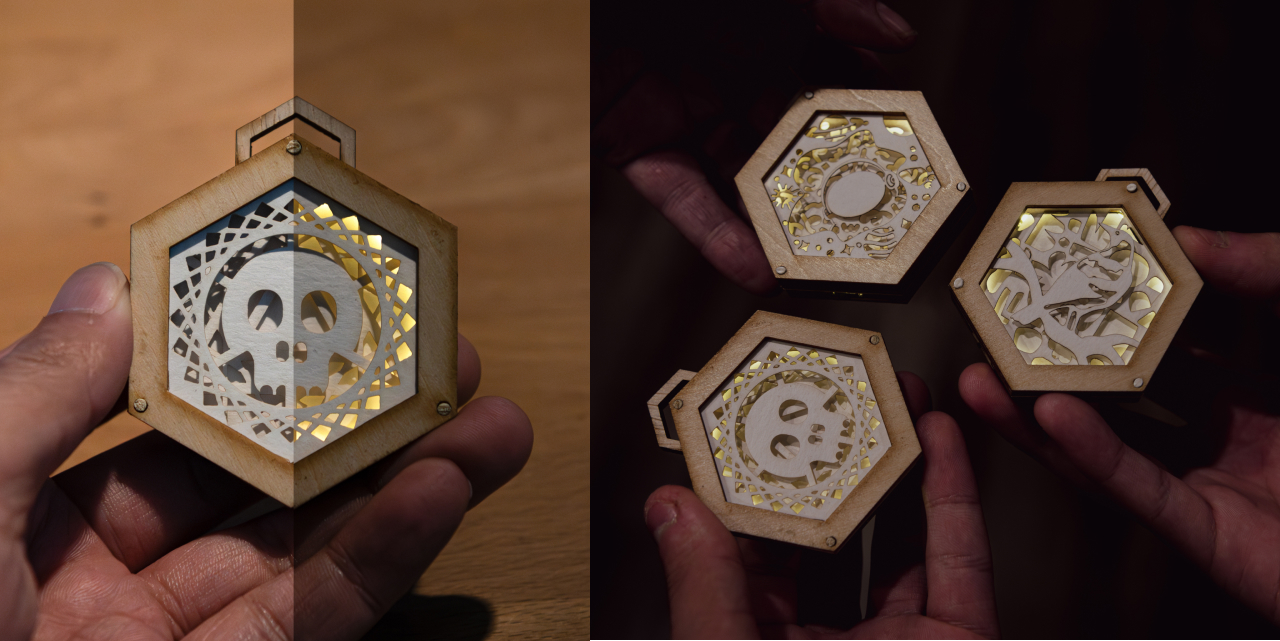
Each Lumogram measures about 55mm.
The cutout designs that formed the backlit ‘diorama’ form the core focus of the Lumogram. As the name suggests, this pictorial composition is left to the participant to construct. This can range from the assembly of whimsical scenes, to more specific goals of co-creating a ‘voice’ for a community. With the new hexagonal layout, the cutouts are now rotatable through 6 directions, allowing for more flexibility in composition.
 cutout designs by [MADA](https://www.monash.edu/mada/about-us/design) Design intern Manaporn Tanwimonrat](/learning-v2/assets/img/lumogram/v2/HERO 5.jpg)
A selection of the COLLECTION.01 cutout designs by MADA Design intern Manaporn Tanwimonrat
Like Lumogram V1, producing an ‘education kit’ that utilised excessive resources was an environmental concern. The selection of recyclable materials and the minimisation of waste offcuts by designing optimised cut paths for the laser cutter contributed to an overall lower energy footprint in producing these kits.
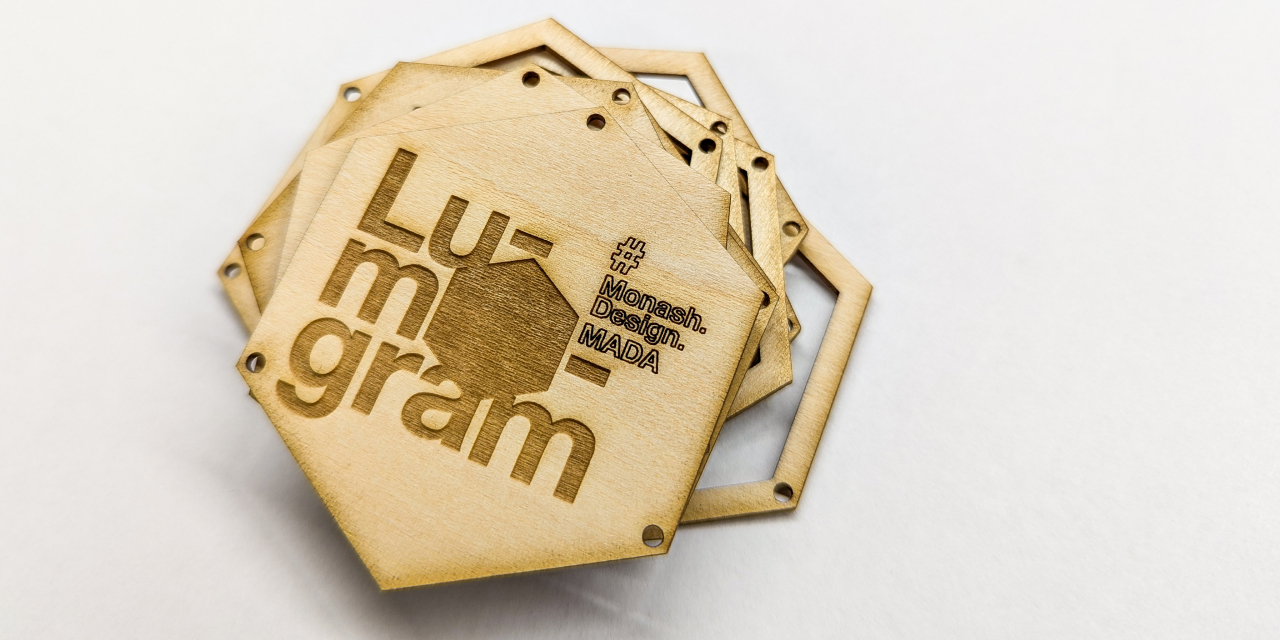
The Lumogram continues to be made from 75% recyclable material, namely, plywood and paper.
Designing for the Community
One of the most significant design intentions of the Lumogram was to allow the potential for customisation, and consequently, to take this project beyond its initial audience of design education. I am looking to collaborate with educators, creative practitioners, non-profits, and communities around the world who wish to introduce the Lumogram as a ‘canvas’ from which they can express their ideas and messages. I believe there is much to learn and share from the co-creation process of the Lumogram’s content.
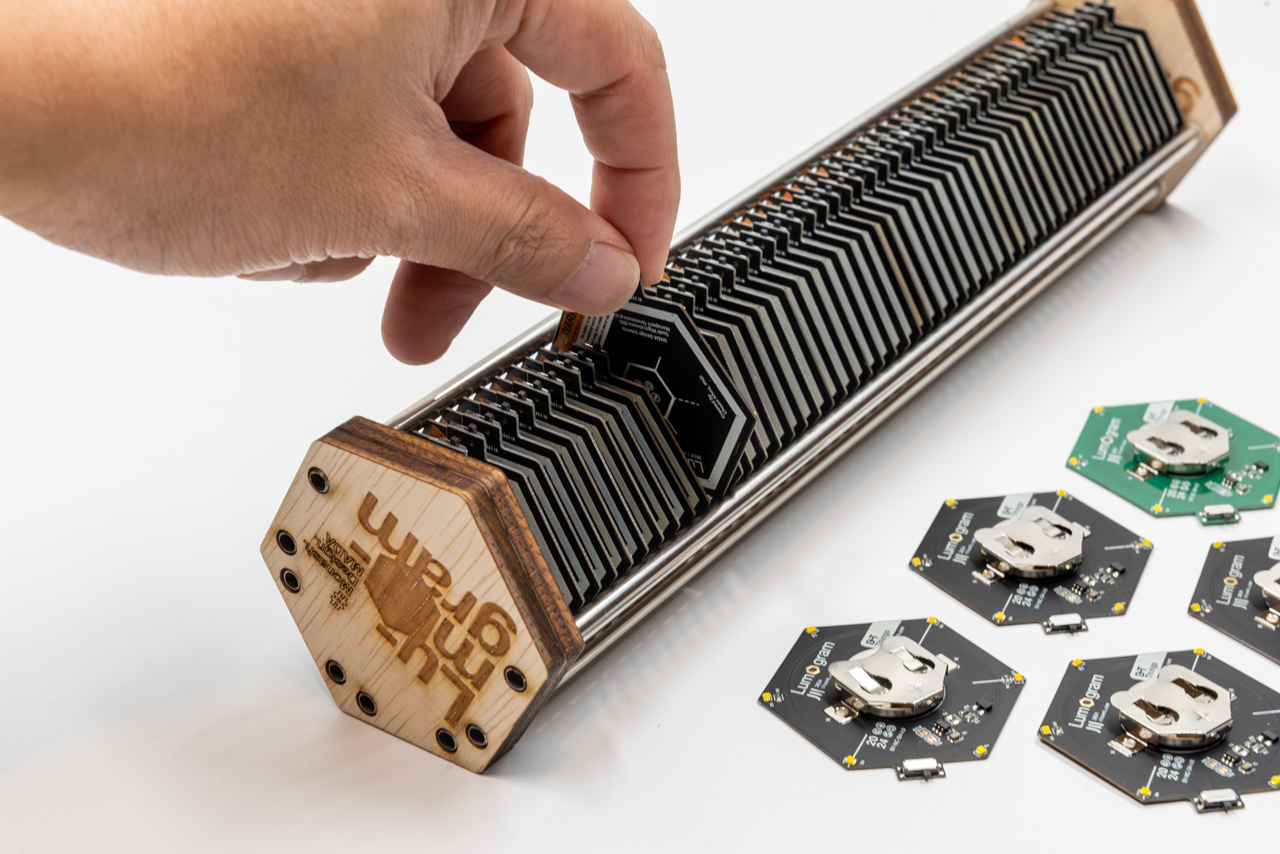
A completed ‘cassette’ of Lumogram PCBs ready for a Design+Technology workshop. An accompanying design lecture and co-design activity rounds up the Lumogram Workshop.
I am organising pilot tests that will allow me to conduct further engagement research and further refine the steps necessary to work at scale. Please get in touch with me if you are keen or have questions!
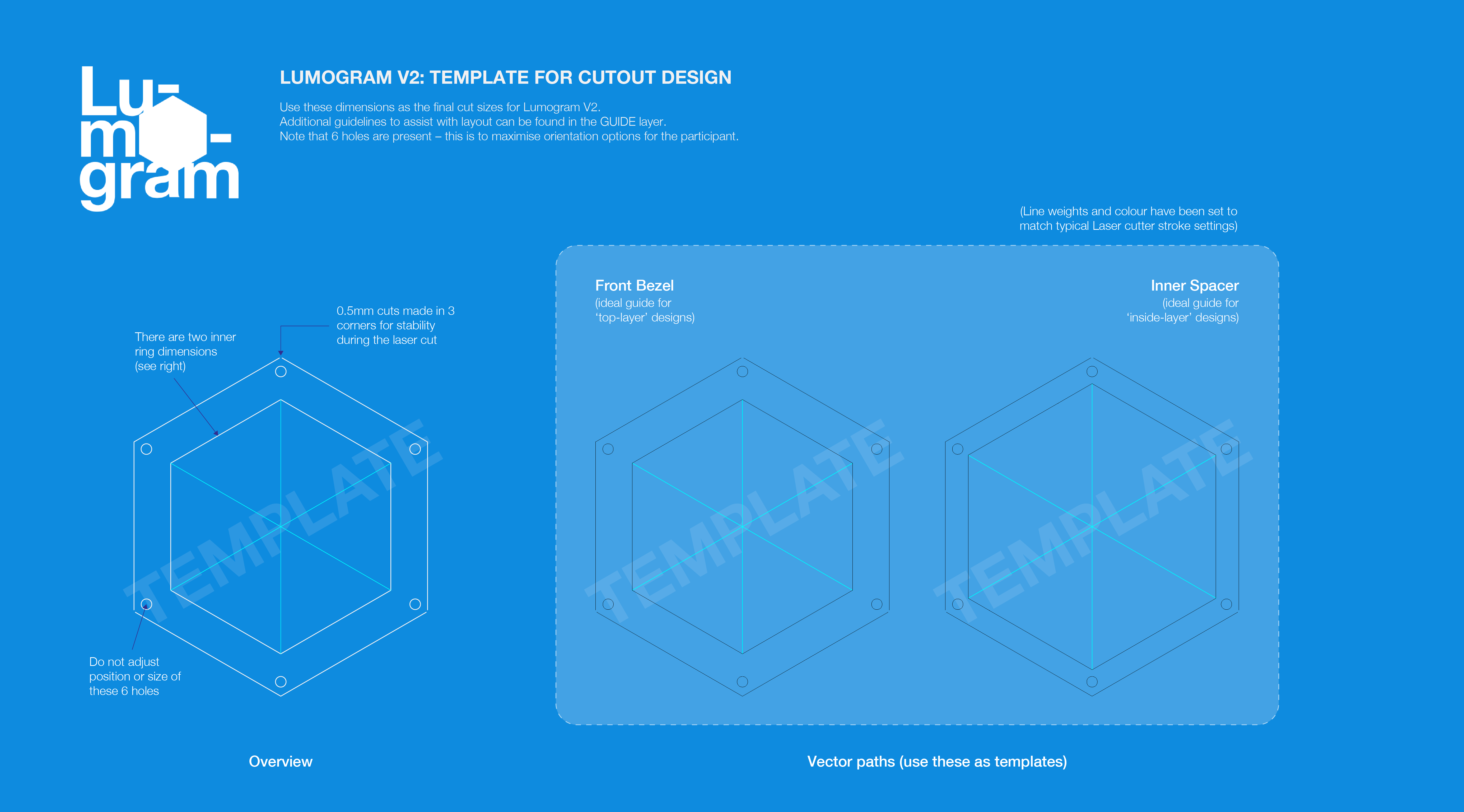
Laser cut templates sized for the Lumogram allow further customisations of the ‘content’ to suit any workshop.
Assembly Videos
Easy-to-follow instructions for assembly have been produced to support the workshops for the V1/V2 Designs:
More details about the V2 Design » The original V1 Design »